CASE STUDY | BUSINESS PROCESS OUTSOURCING
Emerson Improves the Customer Journey with ABBYY Process Intelligence
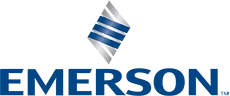
Emerson, a global Fortune 500 company, delivers manufacturer’s software and manufacturing equipment to improve the productivity, safety, and sustainability of the essential industries they serve. ABBYY Process Intelligence guides Emerson in making data-driven decisions for improvements that deliver the highest value in the shortest time.
ABBYY Process Intelligence has helped us make a real cultural change: to rely on data and make data-driven improvements. The data doesn’t lie.
I felt like we were in safe hands being able to leverage the experience ABBYY has had in process mining.
Simon Higgs, Director of Business Transformation and Optimization for Measurement Solutions
Challenge
Emerson’s commitment to continuous improvement for the customer journey had meant using tools like Six Sigma and manual process mapping sessions. Rather than react to various reports and subjective information, they wanted to base improvements on what the actual data from the process indicated. They did due diligence on leading process mining solutions with the following requirements:
- Out-of-the box capabilities
- Intuitive use with coaching available
- Connection with their ERP system
- Best routes through processes
- Bottlenecks and deviations in processes
- A partner with same kind of culture and ethos
Solution
Emerson applied ABBYY process mining to get end-to-end visibility into its high-volume quote-to-cash processes.
ABBYY path analysis shows them the most efficient and cost-effective path and highlights existing variations from it.
Emerson developers use ABBYY process simulation to assess proposed improvements before spending resources to implement them.
The solution is intuitive out of the box—but easily customized to fit specific business challenges.
ABBYY supports them to build out their process and task mining expertise.
Value
- Right out of the box, data can be viewed in “whole new ways” to drive value through the organization.
- Conversations about process improvements and compliance with a standard path are now data-driven.
- Simulation of potential improvements saves time, effort, and expense.